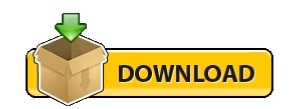

Additive Manufacturing Technologies 2nd edn. Advances in three dimensional printing – state of the art and future perspectives. Depending on the design time of the 3D model, and including time for curing and drying of materials, this procedure can be completed in ∼3 d.ĭimitrov, D., Schreve, K. To illustrate this, we present a detailed procedure for the production of one such reactionware device that will result in the production of a sealed reactor capable of effecting a multistep organic synthesis. This combined approach allows versatility in the design and use of reactionware based on the specific needs of the experimental user. The protocol then further describes the preparation of composite catalyst–silicone materials for incorporation into the 3D-printed device and the steps required to fabricate a reactionware device. The steps of the PROCEDURE describe the design and preparation of a 3D digital model of the desired reactionware device and the preparation of this model for use with fused deposition modeling (FDM) type 3D printers. This protocol describes the printing of an inert polypropylene (PP) architecture with the concurrent printing of soft material catalyst composites, using two different 3D printer setups. We present a general approach for the production of bespoke chemical reactors, termed reactionware, using two different approaches to extrusion-based 3D printing. In recent decades, 3D printing (also known as additive manufacturing) techniques have moved beyond their traditional applications in the fields of industrial manufacturing and prototyping to increasingly find roles in scientific research contexts, such as synthetic chemistry.
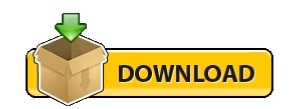